Klip House
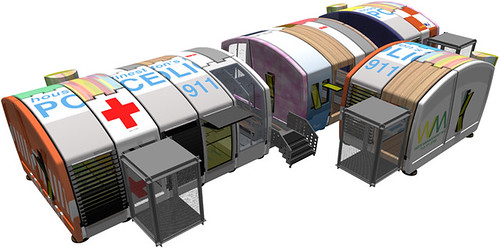
The Klip House by Texan architects Interloop is a project dating back to 1997-2001. The architects describe it as "a delivery system that provides the physical and operational infrastructure for trade corporations to participate in the production, delivery, and servicing of housing."
Not limited only to housing, however, the Klip system was seen as being just as easy to use for hospitals, police stations, and more—even, why not, a pink auto-detailing shop.
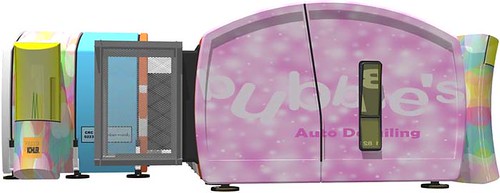
At the time, Interloop had become "frustrated," they explain, by "Federal and State initiatives that provide financial assistance to qualified families and individuals by awarding housing 'vouchers' to serve as the down payment on a house. In its current format, the voucher system distributes a mass of capital such that one voucher equals one house." However:
- We were, and are, frustrated with a design system that is constricted by insurance companies, loan officers, municipalities, and contractors, etc. and decided to look at the overall economic impact that these vouchers might have if they were bundled, rather than distributed. Instead of designing a single house that has very little impact to the housing industry, we worked with the idea of consolidating the vouchers to pay for a housing platform, or infrastructure. We needed to work outside of the home mortgage process in order to gain some ground.
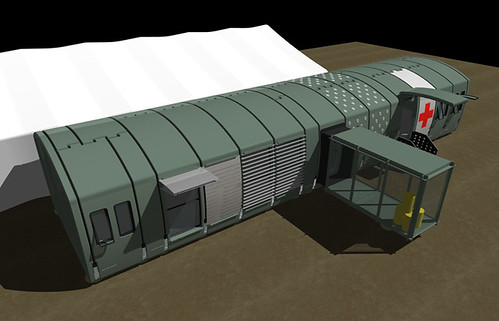

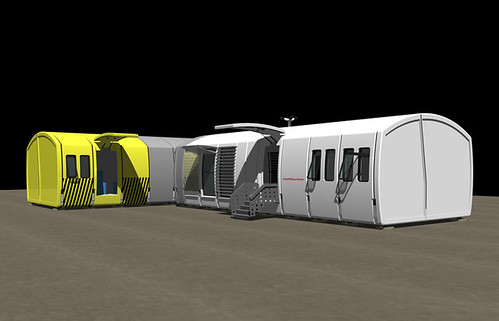
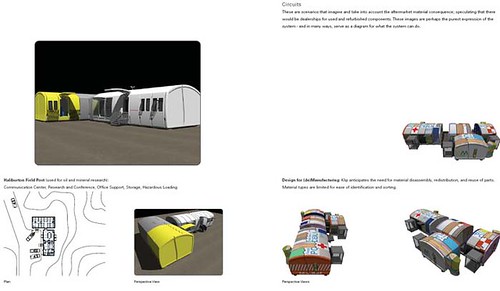
Klip House, seen here, "is essentially engaging financing systems that exist in automotive and product industries"—a statement which comes with a slight twinge of nostalgia for those heady, Greg Lynn-inspired days of the late 1990s when automobile assembly was the reigning model for cutting-edge architectural thesis projects. If your BMW could be assembled offsite and to your every specification, down to heated seats, aerodynamic rear spoilers, and the perfect JBL sound system, why couldn't the architecture you live in follow suit?
Seamless, robotic, and delivered perfectly on schedule, the modular assembly of housing—borrowing assembly line techniques taken from Ford, Saturn, or Lexus—was to lead the way to our architectural future.
In any case, the Klip house itself was at least partially inspired by the boot clips of skis and snowboards. That is, its foundation would operate through a terrestrial "binder," or "adjustable footing system," onto which new rooms or components could be clipped (thus the house's name).
The binders thus allow for "an open array of housing components [to] be added, released, interchanged, upgraded and rearranged" at will. "The architectural contribution," Interloop points out, "is simply to introduce a single enabling technology, i.e. the binder, to generate or illicit response."
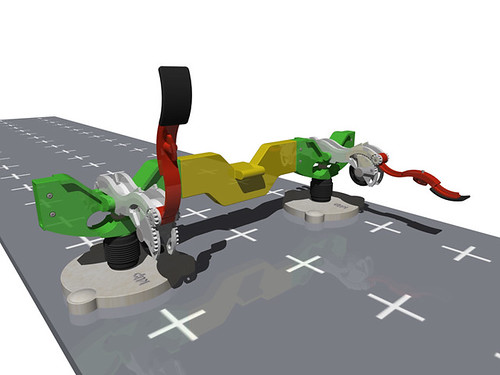
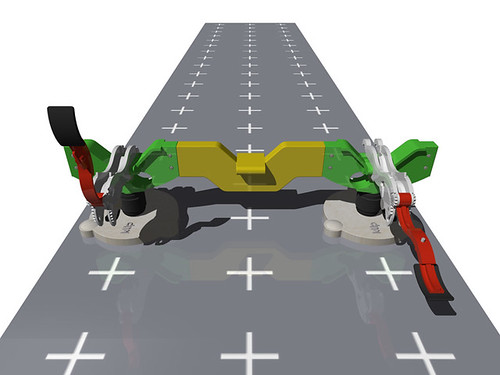
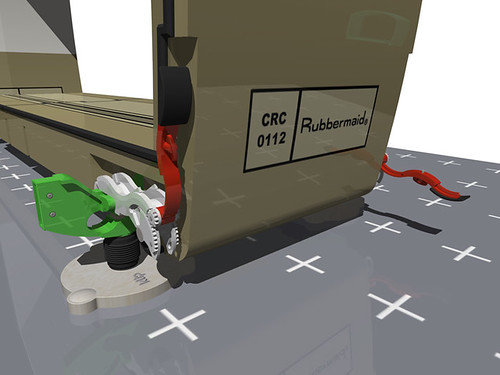
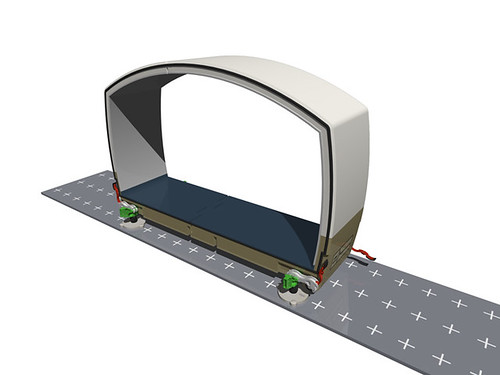
Further, the Klip's "components are available in three and six foot widths, each made with a variety of options and upgrades," and they can be either purchased or leased. This adds a Smart Car/iPod-like personalization to the housing design and procurement process.
Your house, hospital, police station, nightclub, field kitchen, mobile writing lab, counterfeit university space, or auto-body shop can thus be expanded (or shrunken)—let alone recolored, retextured, and resurfaced—based on immediate personal and economic needs.
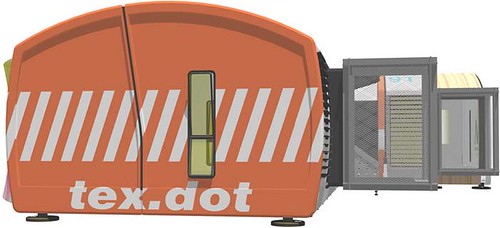
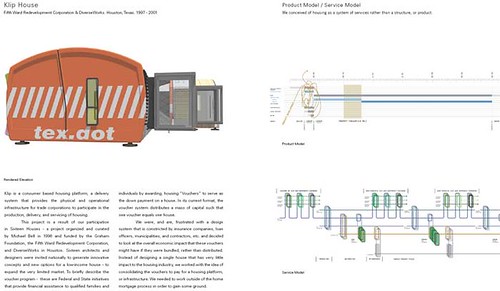
Read more at the architects' website.
Comments are moderated.
If it's not spam, it will appear here shortly!
love
I live in an area with a fair bit of factory built housing. There are a lot of single wide and double wide units, and most of them, particularly the double wides are comparable to stick built housing in most respects. The big difference is in resale value. A stick built shack is often assessed as more valuable than a more comfortable factory built home. I can see a place for modular units like the ones in this post, but they are subject to the same biases and then some, as is no historical sense of how well they hold up to time and weather, how well they can be repaired, and so on.
I think they have the right idea aiming at commercial use which has a shorter time frame than residential and more flexible standards.
Post a Comment